Recursos didácticos
En todas la plantas de proceso se cuenta con una gran variedad de servicios entre los más importantes se encuentra el aire no solo para como medio para modular o modificar la posición de válvulas de control, también lo podemos emplear como medio motriz para accionar algunas bombas de baja capacidad o equipos manuales o bien como medio limpieza.
Para cada caso se requiere una diferente calidad y por lo tanto un tratamiento diferente. El aire como servicio auxiliar lo podemos clasificar según su función en dos tipos:
Aire de servicios:
El aire utilizado para servicios generales tales como limpieza de equipos y piezas durante el mantenimiento, pequeñas bombas neumáticas, arrancadores de motor de compresoras de gas, herramientas neumáticas, sopletes de arena a presión, etc., por lo que los requerimientos de calidad básicos son que esté libre de partículas sólidas que puedan dañar el equipo o pieza que se está limpiado, sin embargo, la presión es un valor importante 7 kg/cm2.
Aire de instrumentos:
Este se emplea como medio motriz en los actuadores de la gran mayoría de las válvulas de control y en algunos casos como medio motriz en bombas pequeñas, por lo que los requerimientos de calidad básicos son que esté libre de partículas sólidas y que tengan una humedad muy baja con el fin de esté no se condense, sin embargo la presión es un valor importante 7 kg/cm2 y una temperatura de rocio de -40°C.
DESCRIPCIÓN DEL SISTEMA DE AIRE COMPRIMIDO
El sistema de aire comprimido es muy habitual en todo tipo de instalaciones industriales; el caso que nos ocupa es el estudio de un sistema de aire comprimido en una planta.
El aire a comprimir es tomado de la atmósfera e introducido en los compresores, donde adquirirá las condiciones depresión adecuadas. Una vez comprimido se hace pasar por los prefiltros, bifurcándose a continuación en dos corrientes: la fracción de aire de servicios se conduce directamente a su tanque de almacenamiento, mientras que la parte del aire destinada a instrumentos es secada y filtrada de nuevo en los postfiltros, para posteriormente almacenarse en el tanque de instrumentos.
El aire comprimido en general es utilizado para el manejo de equipos de planta y para instrumentación. El uso del aire comprimido en equipos de planta hace referencia a dispositivos robustos como taladros, pulidores, elevadores,motores y otros;
Aunque también es utilizado para actuadores de precisión y pequeños motores neumáticos, así como en equipos tales como turbina o calderas y válvulas de control
Estos equipos tienen una función de control de procesos más que de potencia. Debido a la precisión de sus componentes, el aire comprimido usado en ellos ha de tener una calidad superior a la usada en un equipo robusto. Por ejemplo, el aire ha de tener un contenido de humedad tan bajo que su punto de rocío sea siempre superior a la menor temperatura en cualquier lugar de la red con el fin de evitar la presencia de condensados. Además,las impurezas del aire deberán ser menores que 0.1g/Nm3 y hasta un tamaño de 3 g/Nm3.
PREFILTROS Y POSTFILTROS
El aire del ambiente contiene contaminantes que se filtran al compresor, estos contaminantes son concentrados durante la compresión y salen por el sistema de aire comprimido. Un sistema típico de compresión se contamina con partículas sólidas abrasivas como el polvo, residuos de tubería y oxido, lubricantes del compresor, gotas de agua condensada aceite y vapor de hidrocarburos.
Todos los compresores aspiran aire húmedo y sus filtros de aspiración no pueden modificar esto ni eliminar totalmente las partículas sólidas del aire atmosférico.
La humedad es también muy dañina para el sistema ayudando a la corrosión y causando el desgaste excesivo de los componentes. La humedad se acumulará en los puntos bajos del sistema y se congelará durante el tiempo frío, produciendo la detención del sistema y la rotura de líneas.
La humedad llega al interior de la red con el aire que aspira el compresor. La cantidad de humedad depende en primer lugar de la humedad relativa del aire, que a su vez depende de la temperatura del aire y de las condiciones climatológicas. La humedad absoluta es la cantidad de agua contenida en un m3 de aire.
Un filtro ideal removerá toda la suciedad y humedad del sistema neumático sin causar caída de presión en el proceso, o causando la mínima posible
Los sistemas de aire contaminados aumentan los costos de operación al robar energía del sistema de aire; dando como resultado reducción en eficiencia, daños a equipos que operan con aire, mayor mantenimiento y costes de reparación, así como una disminución de la productividad.
Tanto los prefiltros como los postfiltros serán de tipo seco y serán capaces de retener cualquier impureza que pudiera venir en el aire comprimido, en el rango de 1 hasta 3 micras. Las características que deben cumplir los filtros se especifican mediante normas internacionales. En la siguiente tabla se describe la norma ISO para filtros que en la siguiente sección del proyecto describiremos.
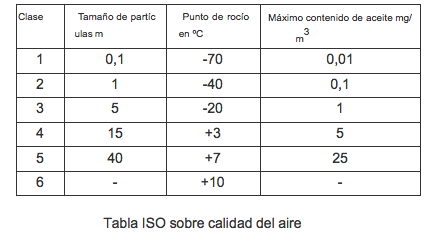
Los prefiltros son comunes tanto al aire de instrumentos como al de servicio, siendo los postfiltros únicamente utilizados para el aire de instrumentos.
El principio de funcionamiento de los pre filtros y post filtros es el mismo. El aire comprimido atraviesa el elemento filtrante desde el interior hasta el exterior. En este proceso las partículas sólidas son retenidas por las diferentes capas que forman el elemento filtrante, mientras que las microgotas de agua que recibe el filtro son eliminadas mediante los dispositivos de purga ubicados en la parte inferior del filtro.
Elementos básicos de una red de aire comprimido
Los elementos principales que componen describiremos a continuación son:
Compresor.
Aftercooler o Enfriadores.
Pre filtro.
Post filtro.
Secadoras/Deshidratadoras de aire.
Tanques o depósitos
Regulación.
Red de tuberías.
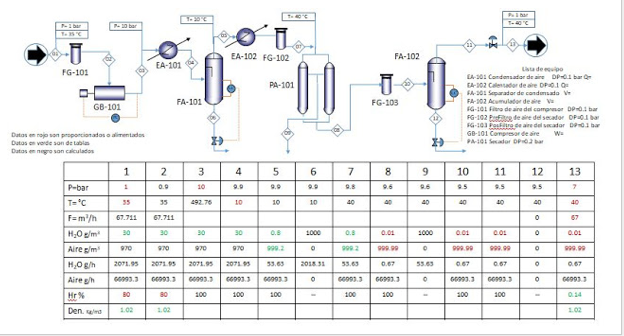
CRITERIOS DE SELECCIÓN DE COMPRESORES.
La selección del tipo de compresor y de su capacidad son parámetros críticos en el diseño de una instalación de aire comprimido. Una acertada elección supone un gran ahorro energético durante el funcionamiento normal de la instalación.
En general, se establecen cinco pasos básicos para fijar correctamente la capacidad del compresor. A saber:
- Estimar el total de consumos de los dispositivos que emplean aire.
- Determinar la presión más elevada que requieren estos.
- Estimar un valor típico de fugas.
- Fijar las máximas caídas de presión admitidas tanto para los diversos elementos como para las conducciones.
- Otras consideraciones que afecten al diseño: condiciones medioambientales, del entorno, altitud, etc.
Como se puede ver todas estas consideraciones son las que hemos ido tomando en pasos anteriores, por lo que sólo queda elegir el tipo más adecuado para aplicación.
Se seleccionará el compresor considerando la presión máxima de operación de este como la Presión necesaria para llegar al punto más alejado de la instalación y aplicándole además un porcentaje de un 15%.
El modelo de compresor más acertado para instalaciones de este tipo es el compresor rotativo exento de aceite, aunque esto también dependerá de las exigencias del sistema de aire comprimido, de la planta y del diseñador de la instalación.
Los compresores son máquinas que tienen por finalidad aportar una energía a los fluidos compresibles (gases y vapores) sobre los que operan, para hacerlos fluir aumentando al mismo tiempo que incrementa su presión.
En esta última característica precisamente, se distinguen de las soplantes y ventiladores que manejan grandes cantidades de fluidos compresibles (aire por ejemplo) sin modificar sensiblemente su presión, con funciones similares a las bombas de fluidos incompresibles.
Un compresor admite gas o vapor a una presión p1 dada, descargándolo a una presión p2 superior. La energía necesaria para efectuar este trabajo la proporciona un motor eléctrico o una turbina de vapor.
Campo de utilización.- Los compresores alternativos (pistón) tienen una amplia gama de volúmenes desplazados en el intervalo, 0.001 a 1000 m3/h, entrando en competencia con los de paletas, tornillo, etc.
En el caso de los compresores para sistemas de aire, estos toma un volumen de aire a presión atmosférica con el fin de incrementar su presión esto con el fin de poderlo utilizar en las plantas de proceso, como fuerza motriz para accionar válvulas de control principalmente y como fuerza motriz para diversas maquinas.
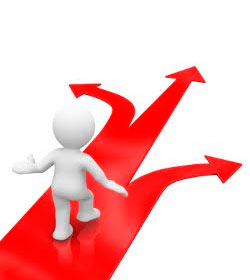